La crescente richiesta di materiali sempre più leggeri e di volumi ridotti nel settore manifatturiero, ha determinato un largo utilizzo di nuove tecniche di produzione, rivoluzionando la velocità con cui è possibile produrre parti e componenti complessi anche molto accuratamente, con significativi progressi nella progettazione di interi sistemi meccanici. In questo processo svolge un ruolo chiave anche l’Ottimizzazione Topologica (TO), tecnica di progettazione che si basa su un algoritmo matematico in grado di eliminare, grazie a criteri di carico assegnati e a vincoli geometrici, parti ridondanti all’interno di un elemento finito. Questo tipo di simulazione consente di raggiungere una nuova distribuzione delle masse e di realizzare quindi modelli più leggeri e performanti.
Accanto all’ottimizzazione topologica, anche l’adozione delle tecniche di Manifattura Additiva (AM) è in continua e veloce crescita. Tra queste, la stampa 3D, si configura come strumento di produzione innovativo, che incide profondamente anche sulle decisioni prese in fase di progettazione, come la selezione del materiale e l’applicazione operativa del progetto. La manifattura additiva è in grado di realizzare oggetti generando e sommando strati successivi di materiale anziché per sottrazione dal pieno, come con le tecniche tradizionali, con vantaggi innumerevoli, primo tra tutti la prototipazione
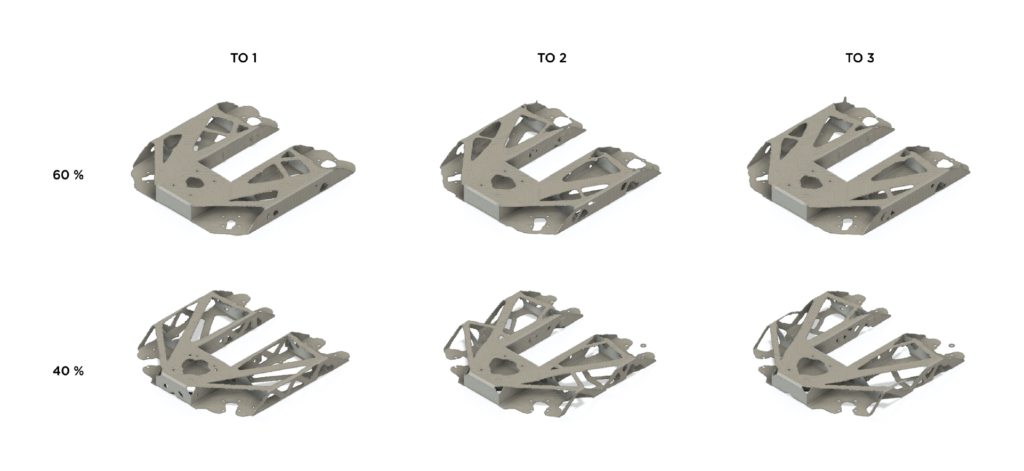
Quali sono i vantaggi di utilizzo di ottimizzazione topologica e stampa 3D?
- Costi e tempi di produzione ridotti;
- componenti realizzati con alta libertà di forma;
- design innovativo e sinuoso, senza i vincoli e limiti delle tecnologie tradizionali.
Ottimizzazione topologica e manifattura additiva per realizzare droni monoscocca
Grazie a un parco macchine per la stampa 3D ci è possibile realizzare internamente prototipi, semilavorati e componenti con funzioni meccaniche e strutturali. In particolare, la combinazione di queste due tecniche è ben applicata a due dei prototipi più importanti della nostra produzione UAV (Unmanned Aerial Vehicle). È il caso del telaio di Helyx, drone FPV (First Person View), progetto pilota che esplora l’implementazione delle tecnologie di progettazione generativa e manifattura additiva, e il più recente Helyx-One, evoluzione di Helyx, il cui telaio è interamente realizzato per sinterizzazione 3D di materiale plastico.
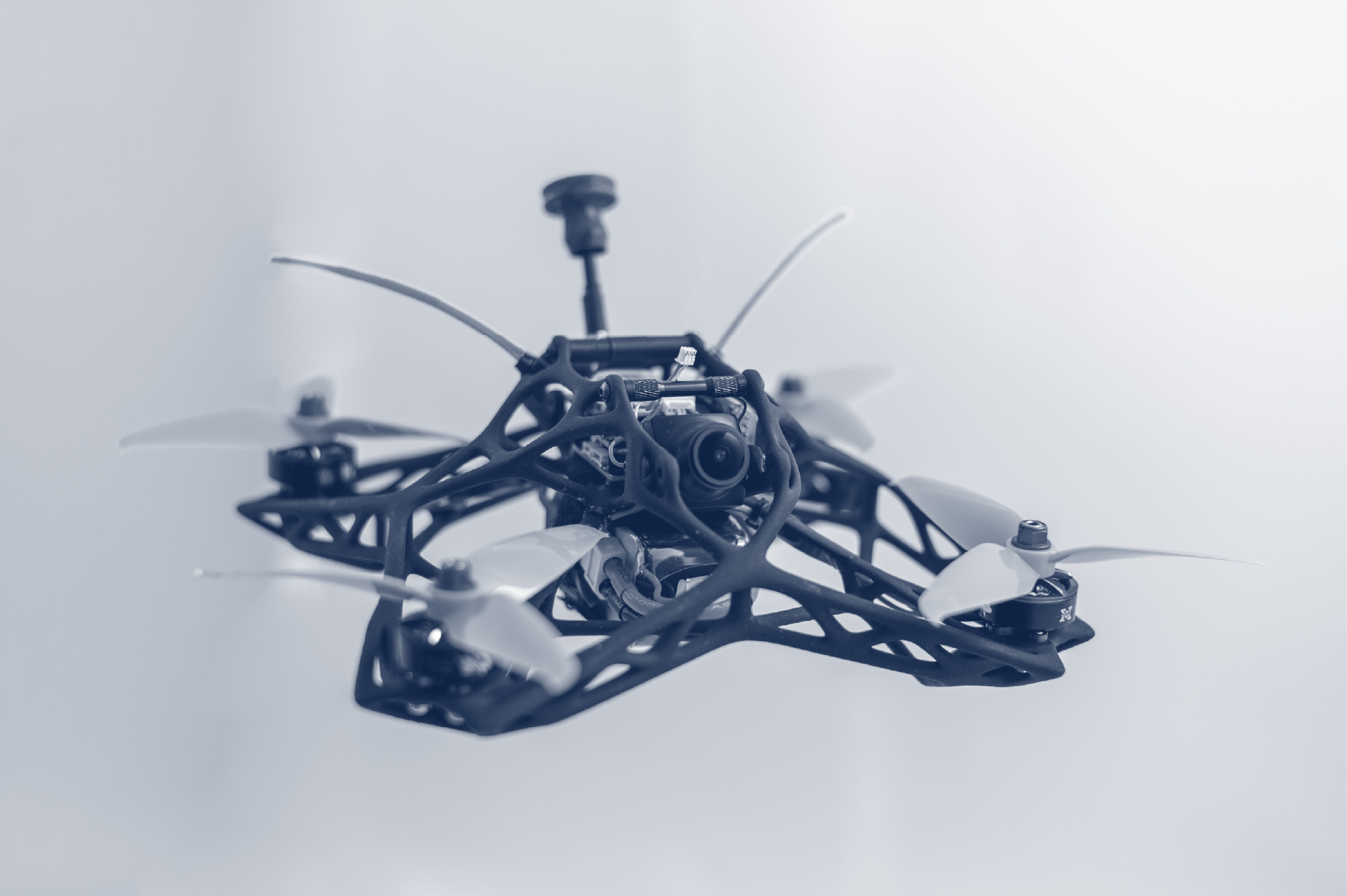
Entrambe le strutture sono progettate con tecniche di design generativo, che determinano una forma unica, robusta ed efficiente dal punto di vista strutturale e aerodinamico in numerosi scenari applicativi, dall’agricoltura di precisione al monitoraggio industriale.
Il telaio di Helyx è oggi un brevetto
In telaio monoscocca per drone da competizione, è caratterizzato da una struttura reticolare che delimita ed avvolge, in corrispondenza della porzione centrale di appoggio, un volume di contenimento delle centraline elettroniche e della batteria in modo da proteggerle da collisioni o urti.
Proprio, Helyx, grazie alla collaborazione con Autodesk e HP, è stato esposto come case study alla fiera di manifattura additiva “Form Next” nel 2018 a Francoforte.
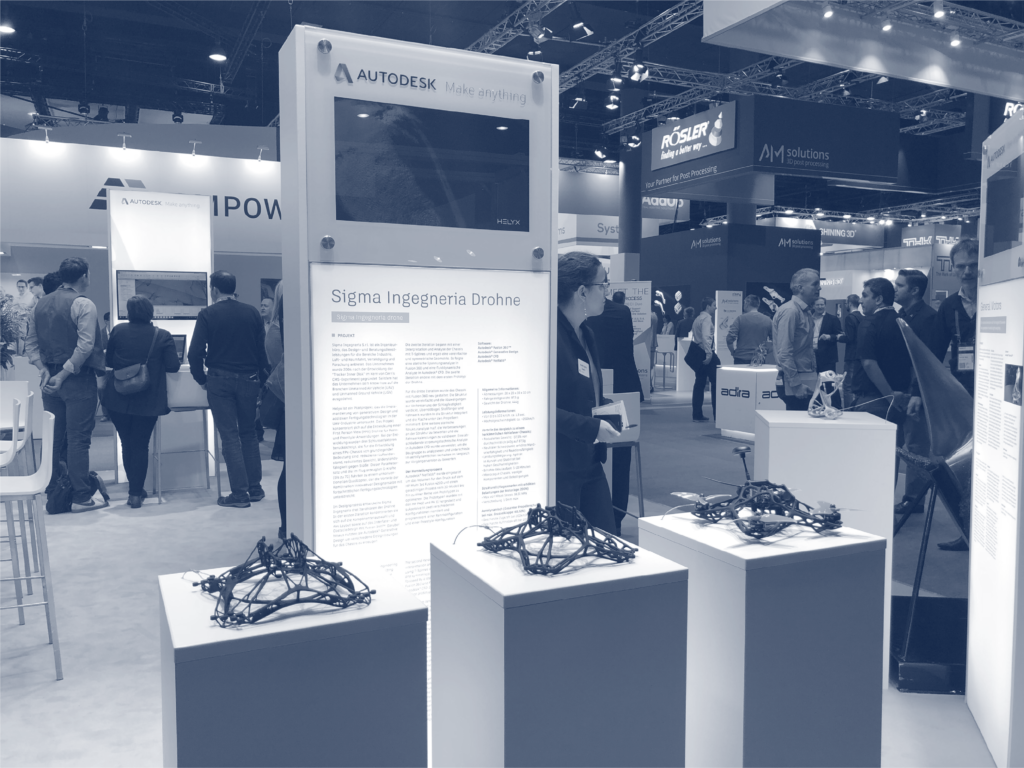
Non solo droni: l’Ottimizzazione Topologica applicata allo studio del telaio del rover
La combinazione di queste due tecniche ha trovato applicazione anche nel progetto di studio per la realizzazione del telaio del rover BMI Focus, sviluppato all’interno di un percorso di tesi magistrale in Ingegneria Aerospaziale. L’obiettivo del lavoro di tesi, era proprio quello di sperimentare la combinazione di tecniche sottrattive tradizionali, come macchine utensili e taglio laser, con tecniche additive (come la stampa 3D) in un processo di produzione ibrido, supportato dagli strumenti di Ottimizzazione Topologica.
Metodi convenzionali a confronto con l’approccio topologico
Nella fase di studio preliminare che ha preceduto la realizzazione del rover, sono stati vagliati tutti i possibili scenari operativi della piattaforma, in termini di caratterizzazione del terreno su cui sarebbe andato ad operare, condizioni climatiche e ambientali, obiettivi di missione e campi di applicazione. Identificate e definite le caratteristiche funzionali e i sottosistemi necessari per il raggiungimento degli obiettivi, si sono infatti ipotizzate due proposte differenti: da una parte un telaio a traliccio saldato convenzionale, basato sui metodi strutturali classici; dall’altra, l’utilizzo delle tecniche di ottimizzazione topologica e manifattura additiva, con il vantaggio di poter sviluppare al meglio tutte le esigenze funzionali emerse dalla fase di analisi preliminare.
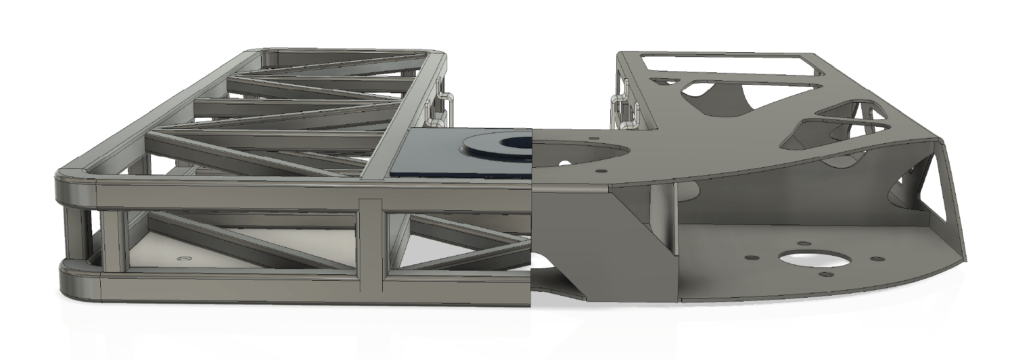
La prima soluzione rappresentava una buona proposta che, dal punto di vista meccanico, è tuttora valida. Tuttavia, considerato l’elevato numero di componenti diversi da saldare, le diverse dimensioni e i requisiti di precisione abbastanza elevati, si è rivelata una soluzione onerosa in termini di costi e tempi di assemblaggio. Per questo motivo, e sulla base di valutazioni di tipo produttivo, è stata perciò proposta una soluzione alternativa che prendesse in considerazione l’utilizzo di lamiere saldate piegate, prodotte in tecnica a taglio laser.
Un processo di produzione ibrido
L’obiettivo per questa nuova soluzione tecnica, una volta selezionato lo spessore appropriato per le lamiere, è stato quello di ottimizzare la struttura risultante mediante l’ambiente di Ottimizzazione Topologica in Autodesk Fusion 360. Dalla geometria di partenza, la fase vera e propria di ottimizzazione topologica con lo scopo di ridurre significativamente masse e volumi finali, ha visto un lungo processo iterativo. Dallo studio e interpretazione dei modelli generati dal software, si è infine raggiunto un risultato affidabile dal punto di vista funzionale e meccanico: una struttura che fosse il più possibile leggera, ma al contempo resistente.
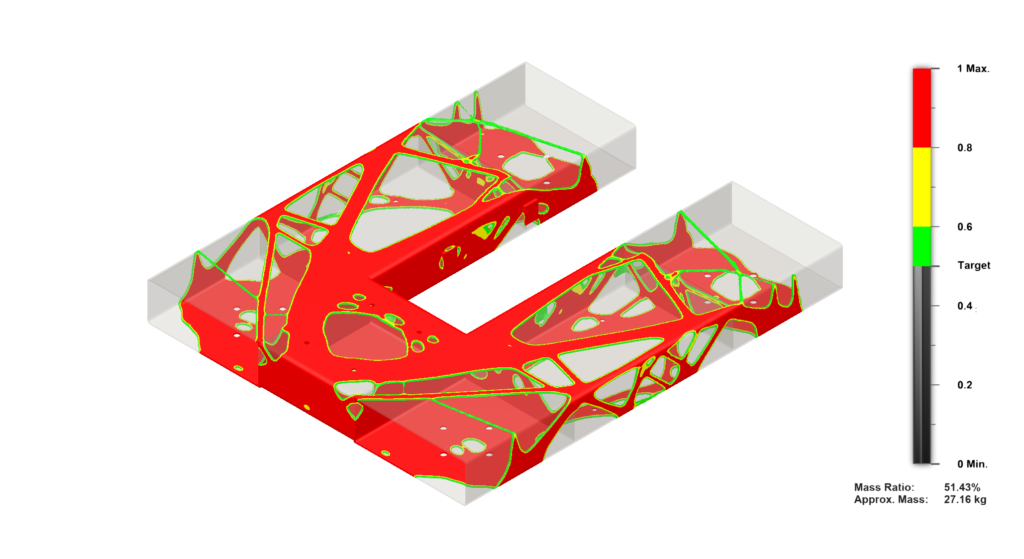
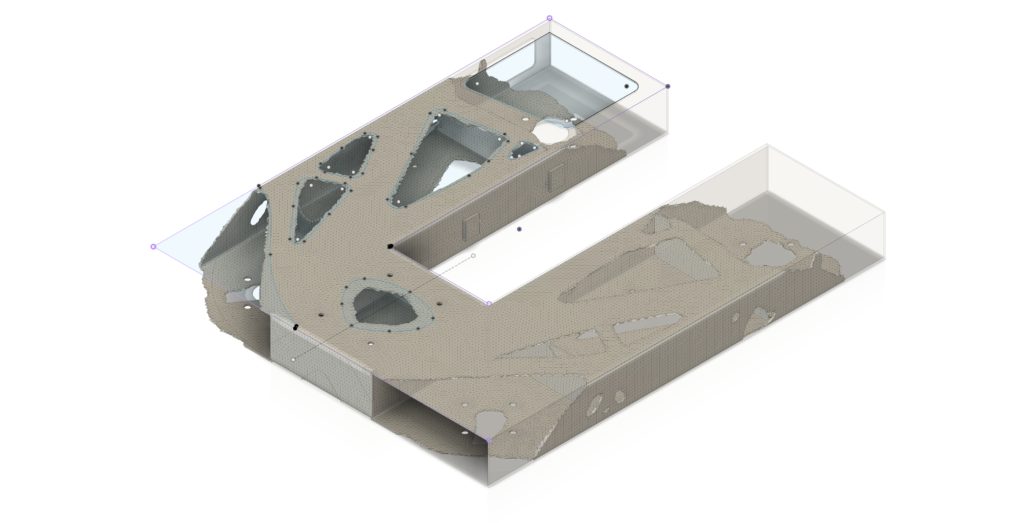
La struttura finale, ottenuta dopo il processo di rimozione delle zone di materiale “superfluo”, si è configurata come una soluzione realizzata in sole cinque parti in semplici fogli di alluminio, di facile realizzazione e trasporto, e semplice da assemblare.
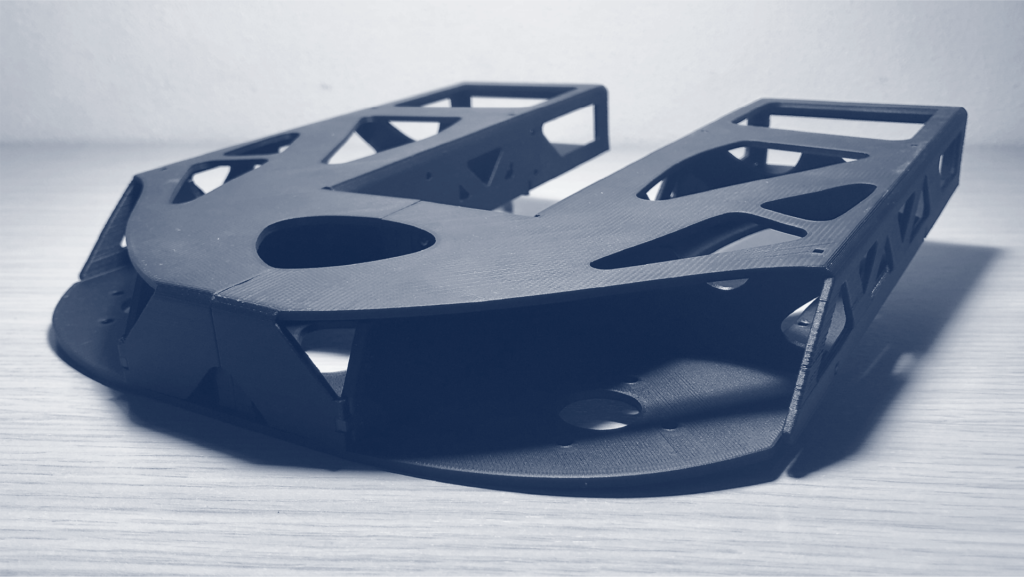
Un nuovo potenziale per la produzione industriale
Le tecniche di Ottimizzazione Topologica e Manifattura Additiva hanno sicuramente stravolto le regole di produzione tradizionale, dando ai progettisti la possibilità di realizzare geometrie del tutto nuove, impensabili fino a poco tempo fa con l’utilizzo dei soli metodi classici, estremamente ottimizzate dal punto di vista strutturale. In quest’ottica la combinazione di TO e AM rappresenta un nuovo metodo di produzione al servizio delle idee focalizzato totalmente sul “cosa” si vuole realizzare, e non più sui metodi di produzione impiegati per farlo. Un nuovo approccio che permette l’elaborazione della forma “migliore”, assolutamente in funzione delle prestazioni che il componente dovrà assecondare.
Tuttavia, va però ricordato che il ruolo del progettista resta fondamentale poiché è lui, guidato sempre da buone intuizioni ingegneristiche, a gestire l’intero processo iterativo nonché a interpretare i risultati generati e valutarli in base alle proprie competenze.